鋼結(jié)構(gòu)箱制作流程通常包括設(shè)計、材料選擇、切割、焊接和組裝等步驟。常見問題包括結(jié)構(gòu)不穩(wěn)固、連接不牢固和防腐處理不當。防腐處理方法流程包括表面處理、底漆、面漆和保護層等步驟,以確保鋼結(jié)構(gòu)箱的耐久性和安全性。
鋼結(jié)構(gòu)箱制作流程
鋼結(jié)構(gòu)箱的制作是一個復(fù)雜且精細的過程,涉及多個步驟,以確保最終產(chǎn)品的安全性和穩(wěn)定性。以下是鋼結(jié)構(gòu)箱制作的主要流程:
1. 設(shè)計
- 詳細設(shè)計:根據(jù)建筑要求和規(guī)范,確定鋼結(jié)構(gòu)箱的具體形狀、尺寸和材料。設(shè)計人員需要考慮使用環(huán)境、載荷和穩(wěn)定性等因素,確保設(shè)計出的結(jié)構(gòu)安全、穩(wěn)定、耐用。
- 圖紙繪制:將設(shè)計細節(jié)轉(zhuǎn)化為詳細的施工圖紙,以便在制作過程中進行實際操作。
2. 材料準備
- 材料選擇:根據(jù)設(shè)計圖紙,選擇合適的鋼板、鋼管和連接件等材料。這些材料需要符合設(shè)計要求和國家標準。
- 材料檢驗:對采購的材料進行質(zhì)量檢驗,確保其符合施工要求。
3. 放樣與號料
- 放樣:根據(jù)施工詳圖或零部件圖樣,按1:1的比例在放樣臺上畫出產(chǎn)品的實體形狀和尺寸,求取實長并制成樣板。
- 號料:根據(jù)樣板在鋼材上畫出構(gòu)件的實樣,并打上各種加工記號,為鋼材的切割下料作準備。
4. 切割
- 切割方法:常用的切割方法包括氣割、機械切割(剪切、鋸切)和等離子切割。選擇合適的切割方法,確保切割邊緣平整、無毛刺。
- 切割精度:切割完成后,需要對切割面進行打磨和處理,以確保焊接質(zhì)量和安全性。
5. 成型
- 冷彎:利用滾圓機、壓力機等設(shè)備將鋼板或型鋼彎制成所需的形狀。冷彎后零件的自由尺寸的允許偏差應(yīng)符合相應(yīng)的規(guī)定。
- 熱彎:將鋼材加熱到1000℃~1100℃后進行煨彎,并在500℃~550℃之前結(jié)束,確保鋼材的質(zhì)量不受影響。
6. 矯正
- 火焰矯正:利用火焰對鋼材進行局部加熱,使其產(chǎn)生壓縮塑性變形,從而達到矯正的目的。
- 機械矯正:通過專用矯正機使彎曲的鋼材在外力作用下產(chǎn)生過量的塑性變形,達到平直的目的。
- 手工矯正:采用錘擊的方法進行,適用于矯正尺寸較小的鋼材。
7. 邊緣加工
- 鏟邊:消除切割造成的邊緣硬化,確保棱角垂直誤差不超過弦長的1/3000,且不大于2mm。
- 刨邊:使用刨邊機對鋼板邊緣進行加工,一般刨邊加工余量為2~4mm。
- 銑邊:使用銑邊機對鋼板邊緣進行加工,工效高,能耗少。
8. 制孔
- 鉆孔:使用鉆孔機在鋼板或型鋼上鉆孔,適用于各種厚度的材料。
- 沖孔:使用沖孔機在較薄的鋼板或型鋼上沖孔,孔徑一般不小于材料的厚度。
9. 組裝
- 初步組裝:將切割和成型后的鋼材按照設(shè)計要求進行初步組裝,使用高強度螺栓進行連接,確保連接牢固可靠。
- 精調(diào):對初步組裝的構(gòu)件進行精調(diào),確保各部分的位置和精度符合設(shè)計要求。
10. 焊接
- 焊接工藝:根據(jù)設(shè)計要求,對鋼材進行焊接處理。焊接過程中采用合理的焊接工藝和焊接參數(shù),確保焊接質(zhì)量和焊接效率。
- 焊接檢測:對焊接完成的構(gòu)件進行檢測和試驗,確保滿足設(shè)計要求和使用安全。
11. 防腐處理
- 表面處理:對鋼結(jié)構(gòu)表面進行防腐處理,一般采用油漆或鍍鋅等方式進行防腐。
- 涂裝要求:在防腐處理過程中,保持表面清潔干燥,涂裝時應(yīng)均勻涂刷,避免漏涂和流掛現(xiàn)象。
12. 質(zhì)量檢驗
- 材料檢驗:嚴格控制所有鋼材、焊條、螺栓等材料的質(zhì)量,確保符合設(shè)計要求和國家標準。
- 施工管理:加強對施工現(xiàn)場的管理,確保施工人員按照規(guī)定的工藝流程和操作規(guī)程進行施工。
- 質(zhì)量檢測:在施工過程中進行嚴格的質(zhì)量檢測和驗收,確保每個環(huán)節(jié)的施工質(zhì)量都符合要求。
通過以上步驟,可以確保鋼結(jié)構(gòu)箱的制作過程科學(xué)、規(guī)范,最終產(chǎn)品能夠滿足設(shè)計要求和使用安全。
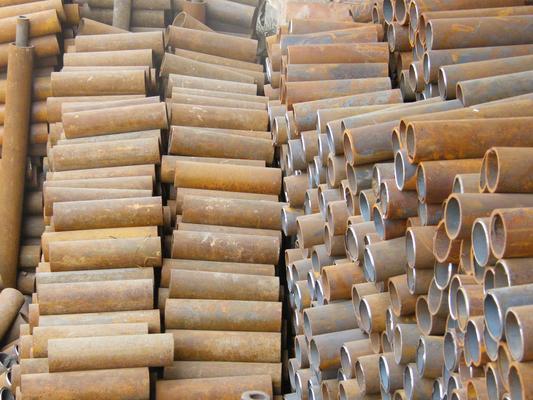
鋼結(jié)構(gòu)箱設(shè)計要點
鋼結(jié)構(gòu)箱材料選擇標準
鋼結(jié)構(gòu)箱制作常見問題
鋼結(jié)構(gòu)箱防腐處理方法
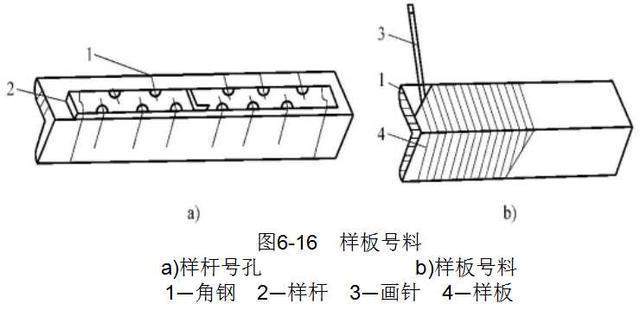
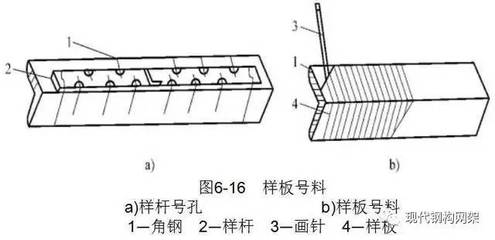
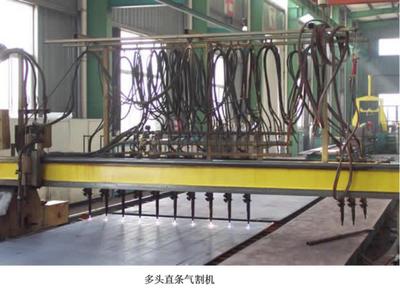
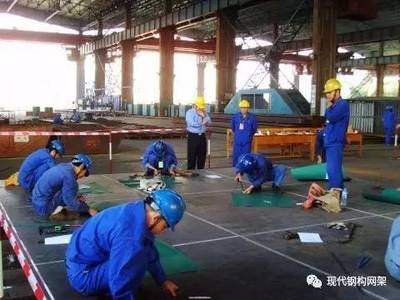